IDENTIFICATION NUMBER 2264
ENTRY CATEGORY (2)
ENTRANT ROLE (Designer /Engineer/ Fabricator and Installer)
APPLICATION OF PROJECT: Restaurant roof, recycled water collection and décor
PROJECT NAME: Trinity Point Tension Membrane Structure 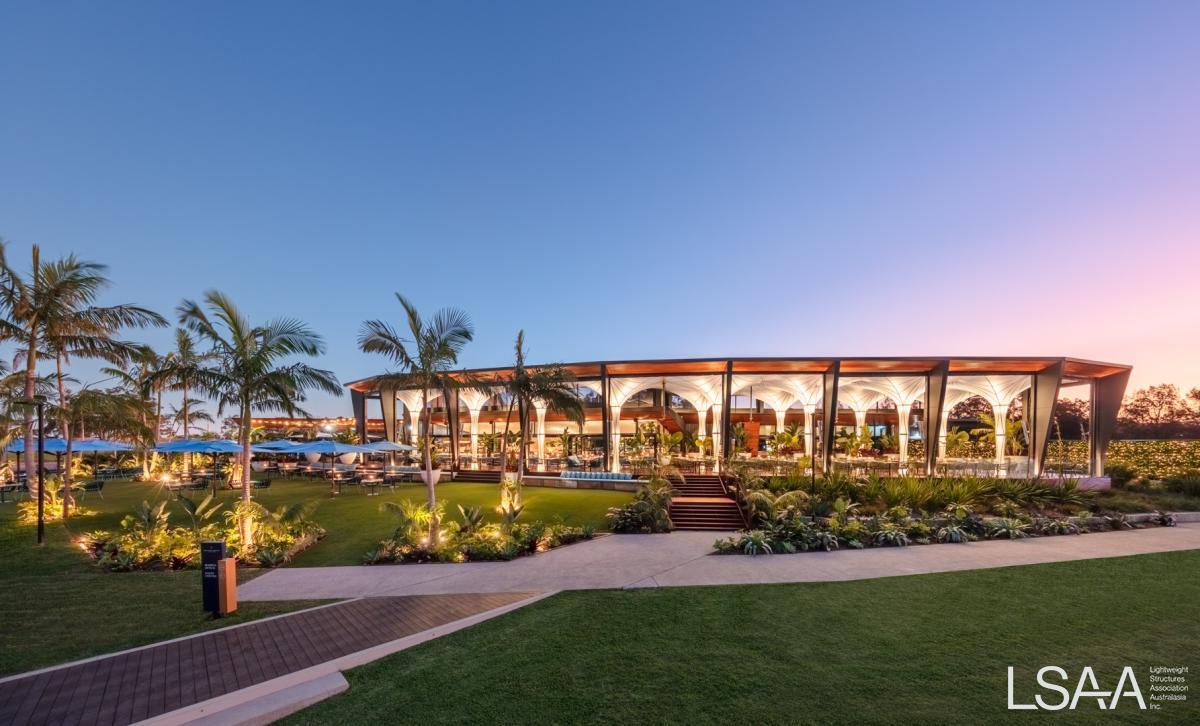
PROJECT DESCRIPTION:
This project was located in the Central Coast of New South Wales. It is a unique tension membrane structure designed to create a wow factor for a new restaurant. It was not only designed to create a visual impact, but also to provide extensive coverage to maximise the outdoor dining area table space and increase revenue for the restaurant.
We were approached by the client to bring a design vision to life. The initial vision of the client to produce this project had come to a halt, then we were asked to come on board to use our expertise to bring this project to fruition and create a visual impact that would create global publicity for the restaurant.
2024 LSAA Design Awards Entry #4866 Link at Langley
IDENTIFICATION NUMBER |
4866 |
ENTRY CATEGORY (1-6) |
4 – Glazing & Vertical Structures |
ALTERNATE CATEGORY (1-6) |
3 – Large Structures |
ENTRANT ROLE |
Designer / Engineer / Fabricator / Installer |
PROJECT NAME: |
Link@Langley ETFE Atrium |
APPLICATION OF PROJECT: |
Clear ETFE ‘glazed’ Atrium Roof over a commercial redevelopment |
PROJECT DESCRIPTION:
The Link@Langley ETFE Atrium not only enhances the visual appeal of the riverside redevelopment but also demonstrates the successful fusion of modern lightweight glazed roof design with practical engineering solutions.
The result is a harmonious blend of form and function and a symbol of innovation, seamlessly integrating into its surroundings while offering a captivating architectural aesthetic. This project exemplifies the power of clever design and cutting-edge materials in shaping the future of urban architecture. Massive in size and scope, the Link@Langley ETFE Atrium structure is 65 meters long and 40 metres wide and sits atop a former office building between seven and eight storeys above the atrium floor.
2024 LSAA Design Awards Entry #3865 Sydney Football Stadium Roof
ID NUMBER |
3865 |
ENTRY CATEGORY |
3 Large Structures |
ENTRANT ROLE |
Design / Engineer / Fabrication / Installation |
PROJECT NAME: |
Sydney Football Stadium Roof |
APPLICATION: |
Tensile Membrane Stadium Roof |
PROJECT DESCRIPTION:
The Sydney Football Stadium Roof, completed in 2022, has joined the growing list of major international iconic stadiums featuring lightweight tensile membrane roofing. Right from the start of the design phase, the project brief emphasised the integration of key stadium elements – the Stadium Domain, Seating Bowl, Façade, and Roof – into a cohesive architectural language.
The highly visible 26,000 square metre tensile membrane roof uses Chukoh Skytop FGT800 PTFE as the primary cladding element. The lightweight PTFE membrane provides exceptional durability and strength, ensuring a 50+ year lifespan with minimal maintenance.
PROJECT NAME: National Throws Centre of Excellence
PROJECT DESCRIPTION:
Fabritecture was contracted for the design and construction of a Serge Ferrari TX30 throws run up canopy for the State Athletics Facility at the Queensland Sports and Athletics Centre (QSAC) in Nathan, Queensland. The tensile building was built to house discus and hammer throwing. The result is a stunning and functional canopy that enhances the sports complex and provides a world-class facility for athletes to train and compete in.
2024 LSAA Design Awards Entry #2862 Wangun Amphitheatre
ID NUMBER |
2862 |
ENTRY CATEGORY |
2 MEDIUM STRUCTURES |
ENTRANT ROLE |
Designer / Engineer / Fabricator / Installer |
PROJECT NAME: |
Wangun Amphitheatre |
APPLICATION: |
Communal performance and meeting space |
PROJECT DESCRIPTION:
Commissioned by the Gunaikurnai Land and Waters Aboriginal Corporation (GLaWAC), the Wangun Amphitheatre stands as a beacon of cultural celebration and architectural excellence. This remarkable circular meeting space features five elliptical tensile membrane canopies representing the Gunaikurnai clan shields, and a striking delta-shaped stage canopy inspired by the iconic boomerang, wangun in the Gunaikurnai language.
IDENTIFICATION NUMBER 5874
ENTRY CATEGORY (1-6) 5 ALTERNATE CATEGORY (1-6) 6
ENTRANT ROLE: Fabricator
PROJECT NAME: Metro Sports Facility
APPLICATION OF PROJECT: Interior acoustic membrane
PROJECT DESCRIPTION:
Fabric Structures was instrumental in the development of the Metro Sports Facility in Christchurch, focusing on the design, engineering, procurement, and installation of a custom ceiling panel solution for the aquatic center. Our task was to create a ceiling system with dual functionalities: an acoustic layer on the underside facing the pools to absorb sound and reduce echo, and a solid membrane on the top side to support the plenum area above. We worked closely with architects and engineers to ensure the panels met both aesthetic and functional requirements. Our precise engineering and installation processes delivered a high-quality solution that enhanced the acoustic environment while maintaining structural integrity. This project showcases our capability to provide innovative fabric solutions tailored to complex needs, contributing significantly to the Metro Sports Facility’s role as a leading sports and recreation venue in Christchurch.
APPLICATION OF PROJECT: Sports Court Canopy
PROJECT DESCRIPTION:
A specialised canopy structure was commissioned for the Field of Dreams project at Oxford Falls Grammar School in New South Wales, Australia. The design aimed to provide weather protection for two competition playing courts situated on the upper level of a two-story building, covering 2,200 square metres.
In addition to the canopy made of PTFE, stainless steel mesh was incorporated around the perimeter of the open-air facility. The rated mesh effectively enclosed the area and acted as a barrier to prevent equipment from falling through and provided fall protection for users of the courts all while maintaining adequate air circulation.
2024 LSAA Design Awards Entry - #5000 Narre Warren Metro Station- Cable Truss Ceiling Support
IDENTIFICATION NUMBER 5000
ENTRY CATEGORY (1-6) 5
ENTRANT ROLE Specialist D&C Subcontractor
PROJECT NAME: Narre Warren Metro Station- Cable Truss Ceiling Support
APPLICATION OF PROJECT: Cable Bow truss and secondary framing supporting ceiling and PID screen.
PROJECT DESCRIPTION:
How 3 Tons of Steel & Cable Replaced 30 Tons of Structural Steel: A New Era in Sustainable Infrastructure
On March 28th, 2024, the newly reconstructed metro stop at Narre Warren station, a critical junction on Melbourne’s Pakenham Line, was officially opened to the public. This station, one of the busiest along the line, had long been plagued by a hazardous and congested rail-road crossing. The recent rebuild of Narre Warren Station, now elevated above the streets in a sleek skyline crossing, is a significant achievement in the city’s ambitious Level Crossing Removal initiative.
ID NUMBER 2284
ENTRY CATEGORY 2 – Medium structures
ENTRANT ROLE Designer / Installer
PROJECT NAME: MSU John Goodman Amphitheatre
APPLICATION: Amphitheatre canopy
PROJECT DESCRIPTION:
The MSU John Goodman Amphitheatre stands as a testament to innovative design meeting environmental challenges. Covering 6,792 square feet, and constructed with PVC TX30 material for durability and weather resistance, it offers exceptional acoustics and a versatile venue for concerts, plays, lectures, and cultural events, ensuring a premier outdoor experience for performers and audiences alike.
- #3258 Yarrow Stadium West Stand
- #1861 North Melbourne Primary School Circles
- #4712 - The Bower Tree Restaurant Facade
- #6725 Bank of Indonesia Millennial Function Hall
- #2863 Tumbalong Green Amphitheatre
- #2019 Australian Open Organic Tree Shade Structure
- #1478 Matakana School Canopy
- #3214 Hamilton Workingman’s Club Canopy
- #2589 Green School Kina Project
- #3864 Whitten Oval Indoor Training Facility
- 2024 LSAA Design Awards Entry #0625 Singapore Bird Paradise
- #0857 MPavilion 2022 Melbourne
- #3698 Te Hiku Sports Hub Project
Page 1 of 3